Zu Gast bei Toyota: Backofen, Prüftstand, Windkanal
Ein Blick hinter die Kulissen der Toyota-Fabrik in Köln: Der Weg des TF108 durch die Abteilungen vom Zeichenbrett bis zur Präsentation
(Motorsport-Total.com) - Obwohl die Werksteams in der Formel 1 nicht mehr zu zählen sind und es viele Hersteller unter eigener Flagge versuchen, ist Toyota neben Ferrari nach wie vor das einzige Team, das seine Rennwagen vollständig unter einem Dach fabriziert. Alle andere Werksteams taten sich mit Privatteams zusammen und übernahmen diese, wie zum Beispiel Renault oder BMW-Sauber.
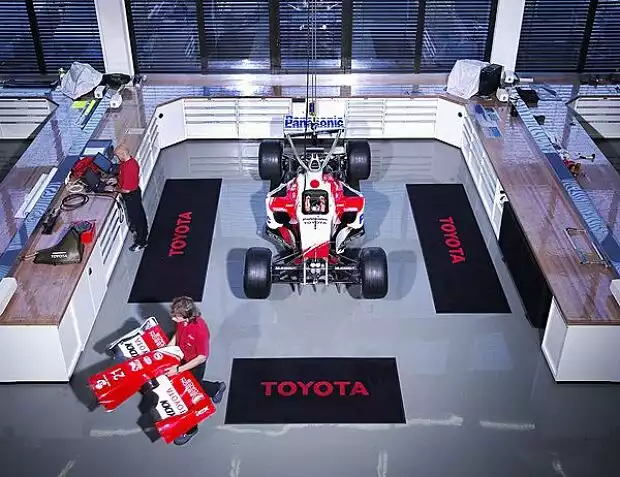
© Toyota
Toyota baut das komplette Auto unter einem Dach: In der Fabrik in Köln
Toyota hat damit einen mutigen Schritt gemacht, denn anstatt auf Bewährtes zu setzen, haben sie ein vollständig neues Team aus der Taufe gehoben. Und nicht nur das: In den "heiligen Hallen" in Köln arbeiten 650 Mitarbeiter aus über 30 Ländern zusammen. "Wir sind ein sehr multi-nationales Team, das schafft Herausforderungen, aber alle bei uns finden das erfrischend", erklärt Präsident John Howett die Philosophie.#w1#
Jarno Trulli passt da als Italiener mit Schweizer Heimat gut in das Kölner Team. Er selbst sieht in der kulturellen Vielfalt keine Schranke, eher einen Vorteil: "In diesem Team begegnet man verschiedenen Leuten aus der ganzen Welt. Das liegt daran, dass man versucht, die besten Leute zu bekommen. Es zählt nur, dass sie gut sind und nicht, woher sie kommen."
Vor Kurzem hat Toyotas jüngstes Kind das Licht der Welt erblickt - der brandneue TF108, mit dem die Japaner die neue Saison in Angriff nehmen wollen. Für einen außenstehenden Beobachter mag das so aussehen, als wäre der neue Rennwagen quasi aus der Fabrik wie aus einem Ei geschlüpft. Daher gewährt Howett ein paar Einblicke in die Geburtsstätte des Toyota.
Kohlefaser - das Kleid des TF108
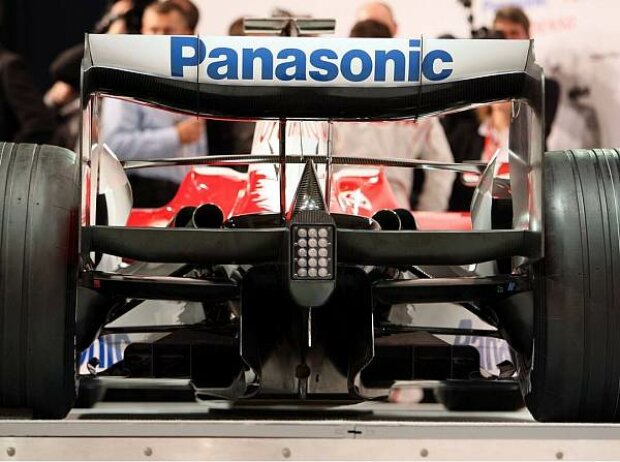
© xpb.cc
Karbon gehört zum Standard-Repertoire der F1-Werkstofftechnik Zoom
Eine der zentralen Einrichtungen der Fabrik sind die Kohlefaser-Backstuben, wo aus dem Hightech-Werkstoff neue Bauteile hergestellt werden, jenem superleichten und superstabilen Material, das in der Formel 1 längst zum Standard gehört. "Das ist eine der wichtigsten Einrichtungen in jedem Formel-1-Team, hier werden die wichtigsten Bauteile hergestellt. Es ist eine der am meisten beschäftigen Werkstätten in der ganzen Fabrik", eröffnet Howett den "Rundgang".
"Hier werden die Designs in reale Komponenten übertragen. Der kohlefaserverstärkte Werkstoff wird präzise von riesigen Bögen abgeschnitten und in die Lay-Out-Werkstatt gebracht. Hier wird das Karbon in speziellen Richtungen ausgerichtet, in eine Matrize eingelegt, um das Bauteil zu verstärken", erklärt der Toyotapräsident.
Anschließend geht es in den Ofen: "Wir verwenden einen Dampfkessel, um das Material unter hohen Druck und Temperaturen zu backen. Diese Öfen laufen 24 Stunden am Tag und sieben Tage die Woche", so Howett und verdeutlicht so den Aufwand, der hinter dem Formel-1-Projekt steht.
Nebenbei sei noch erwähnt, warum das Karbon in bestimmten Richtungen eingelegt wird. Die Kohlefasern verstärken das Bauteil nur in Faserrichtung, man nennt dieses Verhalten auch "Anisotropie". Daher kann man die Verstärkung bezüglich verschiedener Richtungen auf diese Weise gezielt steuern.
Der Motor - das Herz des TF108
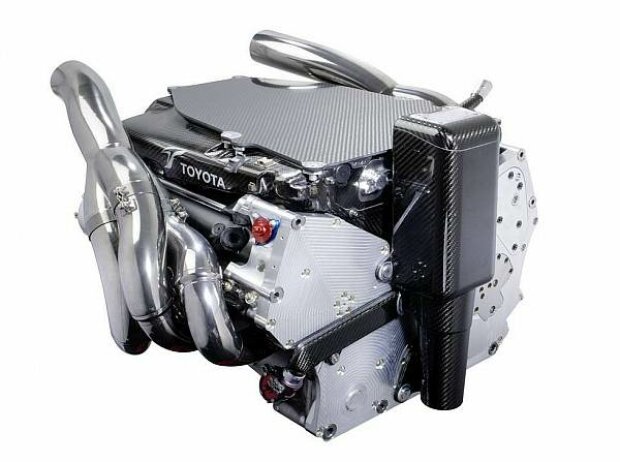
© Toyota
Der RVX-08 wird zusammengeschraubt auf den Prüfstand geschickt Zoom
Diese Arbeit bedarf geschulter Techniker - doch noch geschulter müssen die Motorentechniker sein. Sie kümmern sich um das Herz des TF108, das Triebwerk mit der Bezeichnung RVX-08. "Wir haben sehr fähige Techniker, die an unseren Motoren arbeiten, sie haben wahrscheinlich mehr Fähigkeiten, als ein Schweizer Uhrmacher", so der Toyota-Präsident.
Sobald ein Motor fertig ist, wird er zu den Prüfständen geschickt. Die Motorenentwicklung ist zwar eingefroren, aber die Ingenieure nutzen jedes kleine erdenkliche Schlupfloch im Reglement und finden immer wieder neue Zonen am Aggregat, an denen sie "ganz legal" feilen können. Zudem muss ein Motor nach dem Zusammenbau auf Funktionsfähigkeit überprüft werden und kann auf einen Rennkurs angepasst werden.
"Die fertigen Motoren werden in die Prüfstände eingebaut und dann können wir viele verschiedene Arten von Tests durchführen", fährt Howett fort. "Wir testen neue Entwicklungsstufen, die Kraftentfaltung oder die Zuverlässigkeit und stellen den Motor für die jeweilige Strecke ein. Im Grunde genommen können wir in dieser Einrichtung alles simulieren." Doch der Toyota-Motor war in den vergangenen Jahren nicht die Achillesferse der Formel-1-Rennwagen aus Köln. Viel mehr hat man die Aerodynamik als große Baustelle ausgemacht.
Die Aerodynamik - das Gesicht des TF108
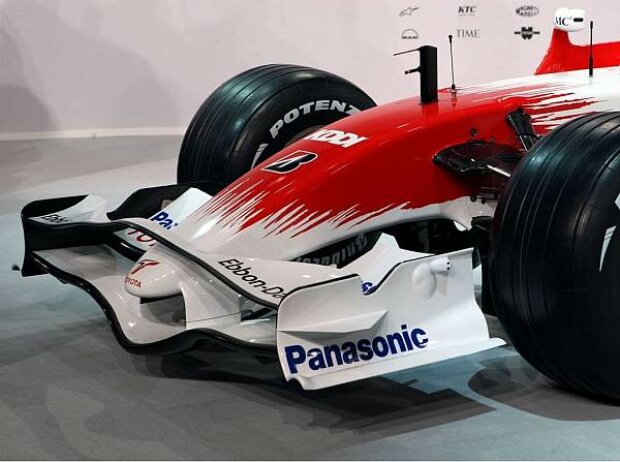
© xpb.cc
Unzählige Windkanalstunden hat dieser Frontflügel hinter sich Zoom
Wichtigstes Werkzeug bei der Erforschung neuer arodynamischer Bauteile und den Luftstromverhältnissen eines Grand-Prix-Autos ist nach wie vor der Windkanal. Doch zuvor entwickelt die Designabteilung neue Bauteile. Mit aufwendigen numerischnen Näherungsverfahren auf Basis der Finite-Differenzen-, Finite-Volumen- oder Finite-Elemtente-Methode simulieren Computer das Strömungsbild des Neuentwurfs.
Wenn die berechneten Ergebnisse den Wünschen entsprechen, geht es in den Windkanal. Dort kommt ein Modell zum Einsatz, welches gerade mal halb so groß ist, wie das reale Vorbild. Doch das genügt, um zuverlässige Ergebnisse zu erhalten. Würde man Bauteile im gleichen Maßstab im Windkanal testen wollen, müssten die Windmaschinen einen wahren Orkan losbrechen, um realistische Ergebnisse zu erhalten. Der Aufwand wäre zu hoch.
So reicht es, wenn der Wind im Windtunnel mit einer Geschwindigkeit von 50 Metern pro Sekunde oder 180 Kilometer pro Stunde über das Modell pfeift und man erhält dennoch Ergebnisse, die der Realität schon sehr nahe kommen. "Die aerodynamische Komponente eines Formel-1-Wagens ist einer der größten Bausteine zu dessen Gesamtperformance", erklärt Howett.
"Der Windkanal ist eine der geheimsten und am besten geschützten Zonen in jeder Formel-1-Fabrik", beschwört der Toyota-Präsident das Herz der aerodynamischen Abteilung. "Hier werden neue Teile zu einem Modell zusammen gesetzt und gründlich und unerbittlich getestet, damit unser Wagen mehr an Performance gewinnt."
Logistik ist die zentrale Schnittstelle
Doch selbst wenn alle einzelnen Abteilungen funktionieren - ohne eine entsprechend funktionierende logistische Abteilung schafft es ein Wagen niemals an die Rennstrecke. Das ist bei Toyota die Aufgabe von Team-Manager Richard Cregan. Er sorgt dafür, dass alle Wagen, hunderte Ersatz- und Einzelteile und Ausrüstungsgegenstände an die Rennstrecke verfrachtet werden - einschließlich der Team-Mitglieder und seiner selbst.
Selbst an der Rennstrecke ist Cregan noch rund um die Uhr beschäftigt und kümmert sich um den Arbeitsraum, das Essen für die Crew und sonstige Transportangelegenheiten. "Man muss sich klare Ziele setzen. Wenn wir unsere Pläne für das Jahr aufstellen, gelten diese für das gesamte Jahr", so Cregan.
Spannend ist dabei vor allem die Planungsphase: "Sobald die FIA den Rennkalender herausgegeben hat, setzen wir uns mit den anderen Abteilungen zusammen, sehen uns die Daten unserer LKWs an und berechnen, wann wir das Equipment dort haben wollen und so weiter. Dann veranlassen wir das Übrige."
Zehn der 18 kommenden Rennen finden in Europa statt - da ist es für Toyota gut, mit Köln einen recht zentralen Standort zu haben, von dem sich alle Rennstecken von Barcelona bis Monza gut erreichen lassen. Sieben Fahrer transportieren in vier LKWs alles, was das Team an der Rennstrecke braucht, von den Rennwagen bis zu Ersatzglühbirnen für den Hospitality-Bereich.

