Folge uns jetzt auf Instagram und erlebe die schönsten und emotionalsten Momente im Motorsport zusammen mit anderen Fans aus der ganzen Welt
Der Stoff, aus dem man Formel-1-Autos schnitzt
Kohlefaserverbundwerkstoff, von vielen einfach als Karbon bezeichnet, ist der magische Stoff, aus dem die Formel-1-Autos bestehen
(Motorsport-Total.com) - Kohlefaserverbundwerkstoff ist eines der wichtigsten Materialien in der heutigen Formel 1. Fast alle sichtbaren Teile des Autos bestehen daraus: von den Flügeln über die Verkleidung, die Aufhängung und die Sicherheitszelle bis hin zum Monocoque. Das sind nahezu 80 Prozent eines Formel-1-Wagens, woraus sich eine immense Verantwortung für den Hersteller dieser Kohlefaserverbundwerkstoffe ergibt.
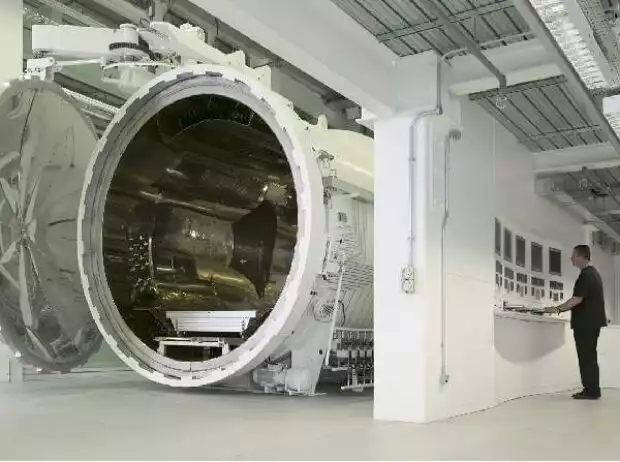
© McLaren
Hitech in der Formel 1: In einem solchen Autoklaven wird Kohlefaser ausgehärtet
Karbons wird wegen seiner einzigartigen Materialeigenschaften eingesetzt. Unter einem Verbund versteht man dabei eine Substanz, die aus zwei oder mehr Materialien zusammengesetzt wird, um im Endprodukt den größtmöglichen Anteil an gewünschten Eigenschaften zu vereinen. Kohlefaser für sich alleine genommen ist bereits eines der härtesten Materialien, das die Natur hergibt, aber seine Stärke besteht in diesem Fall aus der Verbindung mit einem Epoxidharz, wodurch eine größere Flexibilität und ein möglichst geringes Gewicht erzielt wird.#w1#
30 Mitarbeiter nur für die Kohlefaser
Da so viele Bestandteile der Rennautos aus diesem Material bestehen, herrscht in der Karbonverbundabteilung der Formel-1-Teams ein reges Treiben. Mehr als 30 Mitarbeiter umfasst zum Beispiel die Abteilung von Force India, deren Aufgabe es ist, sicherzustellen, dass alle Kohlefaserverbundteile pünktlich, in der richtigen Größe und vor allem in der richtigen Festigkeit hergestellt werden.
Die Abteilung gliedert sich in zwei unterschiedliche Aufgabenbereiche: den Laminating-Shop, wo die jeweiligen Verbunde aufgereiht und in der richtigen Größe zurechtgeschnitten werden, und den Trim-Shop, wo die Teile feingetunt und zusammengesetzt werden. Der größte Teil der Kohlefasern kommt in gerollten Matten an, die in gekühlten Kombischränken aufbewahrt werden - Otto Normalverbraucher würde sie als Kühlschränke bezeichnen -, um ihre Lebensdauer zu verlängern. Diese Kohlefasern wurden bereits mit dem Harz vorbehandelt, sodass sie in diesem Stadium noch flexibel genug sind, um in jene Form gebracht zu werden, in der wir sie jeden Sonntag sehen, aber noch nicht die Starre haben, die sie benötigen, um damit Rennen zu fahren. Das erfolgt in einem späteren Schritt.
Der Vorgang, in dem die einzelnen Produktionsschritte ineinander übergehen, ist ganz genau abgestimmt. Sobald ein Teil fertig designt und vom Zeichenbüro freigegeben ist, kommt es in die Modellabteilung. Diese gibt ihm seine Form und erstellt eine Schablone, um sicherzustellen, dass alle Teile identisch produziert werden. Die Schablone beziehungsweise Form wird dann maschinell exakt auf die benötigte Größe gebracht, bevor sie in den Laminating-Shop geht, wo sie abgedichtet und freigegeben wird. Dadurch wird verhindert, dass die Teile in der Form kleben bleiben, wodurch die Herstellung leichter und schneller erfolgen kann.
Diese Form geht dann in den Laminating-Shop und die Produktion kann beginnen. Einige Kohlefaserteile, wie zum Beispiel das Monocoque, größere Teile de Verkleidung sowie der Unterboden werden außer Haus hergestellt, aber die kleineren Karbonteile werden mühsam von Hand produziert.
Jedes dieser Teile wird dann nach einer Gebrauchsanleitung im Laminating-Shop aufgelegt. Diese Gebrauchsanleitung ist ein richtiggehender Leitfaden, der beschreibt, wie jedes Teil zusammengesetzt wird und am Ende aussehen sollte, um sicherzustellen, dass alle Teile gleich beschaffen sind und dieselben Eigenschaften aufweisen. Nach diesem Vorgang wird das Kohlefaserteil in eine Vakuumtasche gepackt, aus der die Luft herausgesogen wird, um dann in einem Autoklaven oder einem riesigen "Backofen" zu verschwinden, der hohe Temperaturen und Druck erzeugt. Ein Nasenkegel zum Beispiel wird über zwei bis drei Stunden auf 135 Grad Celsius erhitzt, bei einem Druck von 35 psi.
Ab in den Backofen!
Verschiedene Teile benötigen verschiedene "Backanleitungen", die jeweils von der beabsichtigten Nutzung abhängen. Hitzeschutzschilde zum Beispiel - jene Kohlefaserteile, die unterhalb der Verkleidung angebracht werden und außergewöhnlich hohen Temperaturen ausgesetzt sind - müssen zwei bis drei Stunden bei 135 Grad und 75 psi gebacken werden. Danach muss jedes Schild 20 Stunden lang bei 180 Grad nachhärten.
Auf ähnliche Weise müssen die einzelnen Teile mit einem maßgeschneiderten Kleber verbunden werden, der den hohen Temperaturen standhält und den Gewichtsbeschränkungen entspricht.
Wenn die Kohlefaserteile schließlich auf die richtige Größe gebracht und abgenommen sind, werden sie unter Rennbedingungen geprüft. Natürlich ist allgemein bekannt, was mit den Kohlefaser passieren kann, wenn der Fahrer ins Kiesbett rutscht oder die Boxenmauer touchiert, weshalb zu jedem Rennen Techniker mitreisen, die sich um die Wartung der beiden Kohlefaserverbundstoffe kümmern.
Nach dem Test werden alle Teile auf Risse untersucht und nochmals überprüft, um sicherzustellen, dass sie erneut verwendet werden können. Beim kleinsten Anzeichen für eine Beschädigung wird das Teil ausgetauscht - das Team kann sich nicht erlauben, das Risiko einzugehen, dass ein Teil bei hoher Geschwindigkeit nicht hält. Man muss nicht erwähnen, dass es schon zahlreiche lange Nächte gab, in denen die Techniker versuchten, neue Kohlefaserteile herzustellen, wenn das Auto einen größeren Unfall hatte.
"Wir haben schon erlebt, dass die Kohlefaserteile komplett zerstört waren", erklärt Brian Snooks, Manager für Verbundwerkstoffe und Zusammensetzung bei Force India. "In solchen Situationen kannst du die Teile nicht reparieren. Das würde zu lange dauern und außerdem wären sie nicht stabil genug, deshalb mussten wir die Teile komplett neu herstellen und rechtzeitig zum Rennwochenende rausschicken. Unter solchen Umständen muss man darauf vorbereitet sein, Überstunden zu machen - und man braucht einen guten Sinn für Humor."

