Der BMW P86/8: Die treibende Kraft
Auch wenn die Motorenentwicklung fast komplett "eingefroren" wurde, hatten die Ingenieure im Antriebsbereich dank der Standardelektronik-Einführung viel zu tun
(Motorsport-Total.com) - Während der BMW V8-Grundmotor seit Ende 2006 homologiert ist und nur noch in der Peripherie weiter entwickelt werden darf, erfahren andere Bereiche des komplett in München unter Regie von Markus Duesmann entwickelten Antriebsstrangs grundlegende Änderungen.
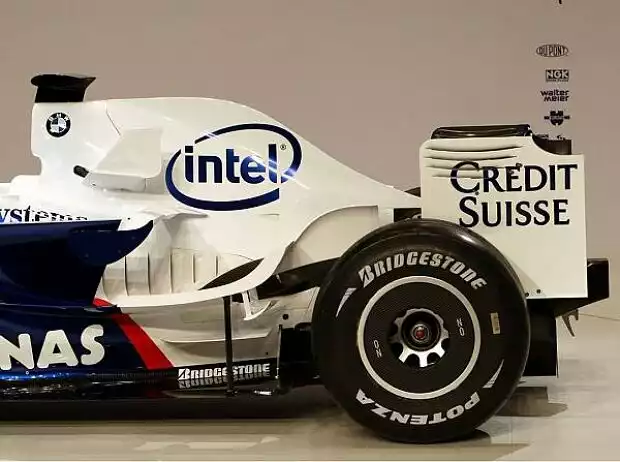
© xpb.cc
Versteckt im Heck arbeitet der Antrieb des BMW Sauber F1.08
Die Getriebe müssen nun an vier aufeinander folgenden Rennwochenenden benutzt werden. Lediglich die Zahnräder und Klauenringe der einzelnen Gänge dürfen pro Event einmal an die Rennstrecke angepasst werden. Dies ist zwingend erforderlich, wenn beispielsweise direkt hintereinander die Rennen in Monaco (Höchstgeschwindigkeit rund 290 km/h) und Montréal (Höchstgeschwindigkeit rund 330 km/h) folgen. Bis auf einige untergeordnete Anbauteile aber, muss das Getriebe nun für ca. 2.500 Kilometer unangetastet bleiben.#w1#
Die Laufleistung ist indes nicht die einzige neue Anforderung: Die Gangzahnräder müssen neuerdings ein Mindestgewicht von 600 Gramm pro Gang aufweisen, ihre Mindestbreite ist auf 12 Millimeter vorgeschrieben, und der Achsabstand zwischen Haupt- und Nebenwellen darf 85 Millimeter nicht unterschreiten. Dies bedeutete eine komplett neue Auslegung des Getriebes und die Anschaffung einer Vielzahl neuer Bauteile, da jene aus dem Jahr 2007 verbliebenen nicht mehr reglementkonform sind.
In einem herkömmlichen Getriebe wird die Antriebskraft zum Gangwechsel für ca. 50 Millisekunden unterbrochen, das Fahrzeug besitzt in dieser Zeitspanne keinen Vortrieb, sondern rollt. Bei den hohen Formel-1-Geschwindigkeiten wird es deshalb durch den aerodynamischen Widerstand während dieses Zeitraumes mit einer Verzögerung von rund 1 g abgebremst. Dies wiederum entspricht bei einem Pkw einem kräftigen Bremsvorgang.
Diese Zugkraftunterbrechungen bei jedem Hochschalten - beim Großen Preis von Monaco passiert dies über die Renndistanz rund 2.000 Mal - summieren sich zu einem erheblichen Zeitnachteil beziehungsweise zu mehreren hundert Metern.
Mit dem BMW G1.08 Schnellschaltgetriebe, kurz SSG, entfallen wie schon im F1.07 die Zugkraftunterbrechungen komplett. Ein ausgeklügeltes Zusammenspiel der mechanischen und elektronischen Komponenten macht es möglich. Eine Hauptaufgabe war hier, diese komplexen Anforderungen an die neue, ab 2008 für alle Teams zur Verwendung vorgeschriebene, Standard-Elektronik-Einheit anzupassen.
Neben der Entwicklung findet auch der Bau des SSG in München statt. Die in diesem Getriebe extrem hoch belasteten Zahnräder werden zum Teil im BMW Werk Dingolfing gefertigt. Sie bestehen aus hochfestem Stahl. Das Getriebe-Gehäuse besteht aus Titan-Guss.
Drehmoment und Drehzahl des Motors zu wandeln, ist dabei nur eine Aufgabe des Getriebes. Außerdem muss es in der Lage sein, die Kräfte des Fahrwerks über den Motor an das Chassis weiterzugeben.
Eine schwarze Box für alle
Auf die zweite grundlegende Neuerung haben die BMW Ingenieure weit weniger Einfluss. Die neue Standard-Elektronik-Einheit wird allen Teams praktisch als schwarze Box mit Gebrauchsanweisung geliefert, mit der man bestmöglich zurechtkommen muss.
In erster Linie bedeutet die Einführung dieser SECU (Standard Electronic Control Unit) den Wegfall der elektro-nischen Traktionskontrolle, die in Kurven und bei Beschleunigungs¬vorgängen die Motorleistung präzise regulierte, um so für minimalen Schlupf und folglich optimale Traktion zu sorgen.
Der im Jahr 2007 sogar für alle Motor-, Getriebe- und Fahrzeugbelange verwendete BMW Race Car Controller (RCC) vereinigte ein Höchstmaß an Funktionalität, Flexibilität und Anpassungsfähigkeit auf alle Fahrzustände mit minimalem Bauraum und Gewicht. Hingegen sind bei der SECU, die von McLaren Electronics Systems geliefert wird, sowohl die elektronische Hardware als auch die Programme vorgegeben.
Diese Umstellung erforderte nicht nur die Überarbeitung der technischen Spezifikationen des Fahrzeugs, sondern grundlegende Maßnahmen in der Infrastruktur und Peripherie - angefangen beim Testfeld mit allen Motor-, Getriebe- und Aggregat-Prüfständen bis hin zu den Applikations- und Auswertewerkzeugen für Telemetrie und Analyse und den Computern in München, Hinwil und an den Rennstrecken.
Viel Kapazität und Aufwand mussten in neue Fahrzeugsysteme investiert werden - beispielsweise in das Lenkrad mit all seinen Kontrollfunktionen, in die Anpassung von Chassis, Getriebe und Motor an neue Sensoren und in eine komplett anders aufgebaute Philosophie und Logik der SECU.
Seit Juli 2007 wird mit der SECU bei BMW in München am Motor- und Getriebeprüfstand gearbeitet, seit Herbst 2007 wird sie in einem Interimsfahrzeug im Test erprobt. Mario Theissen erklärt: "BMW hat ab 2000 die F1-Elektronik komplett im eigenen Haus entwickelt. Dabei spielte das BMW Forschungs- und Innovationszentrum FIZ eine wichtige Rolle. Das gesamte Unternehmen und die Serienfahrzeuge haben von diesen Entwicklungen profitiert, sowohl im Bereich der Funktionssteuerung als auch ihrer Überwachung."
"Insofern bedauern wir die Einführung der SECU. Allerdings kommt für 2009 eine im Reglement bereits festgeschriebene neue Herausforderung auf unsere F1-Spezialisten zu: Wir werden Systeme zur Nutzung der kinetischen Energie entwickeln. Derzeit profitieren wir bezüglich Systemen zur Energie-Rückgewinnung von Entwicklungen der Serie."
"Aber bis zum Saisonstart 2009 werden wir im F1-Tempo Technologien entwickeln, die dann der Großserie einen Vorsprung bringen. Das betrifft beispielsweise Generatoren, Elektro-motoren und Speichermedien. Diese Entwicklungen sind auch für ökonomisch und ökologisch effiziente Straßenfahrzeuge von Bedeutung."
Der Weg zum Homologationsmotor
Die FIA hat die Motorenentwicklung in den vergangenen Jahren drastisch reglementiert. Argumente waren Sicherheit, also geringere Höchstgeschwindigkeiten, und Kostenersparnis. Teil der Reglementierung war eine Vervierfachung der Laufleistung seit 2002. 2003 mussten die Rennen erstmals mit demselben Motor bestritten werden, der zuvor im Qualifying eingesetzt worden war. 2004 galt die Ein-Wochenend-Motorenregel. Ab 2005 mussten die Triebwerke zwei GP-Wochenenden durchstehen. Zugunsten größerer Fahraktivität an Freitagen ist es seit 2007 wieder erlaubt, in den ersten beiden Freien Trainings Triebwerke einzusetzen, die von dieser Regelung ausgenommen sind.
Die Konzeption des heutigen BMW V8-Motors reicht auf den November 2004 zurück. Damals war der Wechsel von V10- auf V8-Motoren zur Saison 2006 beschlossen worden. Gleichzeitig waren auch wesentliche Konstruktions¬parameter reglementiert worden: Neben dem Hubraum von 2.400 ccm wurde für die V8-Motoren auch der Bankwinkel von 90 Grad vorgeschrieben.
95 Kilogramm Mindestgewicht wurden festgelegt - inklusive Ansaugtrakt einschließlich Luftfilter, Kraftstoffleitungen und Einspritzsystem, Zündspule, Sensoren und Kabelbaum, Lichtmaschine, Kühlmittel- und Ölpumpen. Aber ohne Befüllung, Auspuffkrümmer, Hitzeschilder, Öltanks, Batterien, Wärmetauscher und Hydraulikpumpe.
Die Schwerpunktlage des Triebwerks ist seither ebenfalls verbindlich vorgeschrieben: In der Höhe mindestens 165 Millimeter, gemessen wird von der Unterkante der Ölwanne. Auf der Längs- und Querachse des V8 muss der Schwerpunkt bis auf eine Abweichung von ± 50 Millimeter in der geometrischen Mitte des Motors liegen.
Die Zylinderbohrung wurde auf maximal 98 Millimeter limitiert, der Zylinder¬abstand auf 106,5 Millimeter (± 0,2 mm) fixiert. Die zentrale Achse der Kurbelwelle darf nicht weniger als 58 Millimeter über der Referenzlinie liegen. Variable Ansaugsysteme zur Optimierung des Drehmomentverlaufs sind ebenfalls schon seit 2006 verboten.
Die Spannungsversorgung der Motorelektrik und -elektronik ist auf maximal 17 Volt festgelegt. Die Kraftstoffpumpe muss mechanisch betrieben werden. Zur Betätigung des Drosselklappensystems darf nur ein Aktuator dienen. Mit Ausnahme der elektrischen Hilfspumpen im Benzintank müssen alle Nebenaggregate mechanisch und direkt über den Motor angetrieben werden. Zudem wurde eine lange Liste exotischer Materialien ausgeschlossen.
Seither beschränkt man sich auf konventionelle, im Reglement festgeschriebene Titan- und Aluminiumlegierungen. Weitere Einschränkungen folgten 2007. Ab Saisonbeginn galt die Drehzahlbegrenzung auf 19.000 U/min. Ende 2006 mussten alle Teams Triebwerke als Muster einreichen, die zunächst bis Ende 2010 im Wesentlichen unverändert bleiben sollten. Entwicklungsspielraum wurde nur noch für das Motorumfeld eingeräumt, etwa für die Kühlung, Ansauganlage oder die Nebenaggregate. Im Winter 2005 wurde die Einführung der SECU beschlossen.
Vorbereitung auf den Ernstfall
Ehe eine Spezifikation eines BMW V8 P86/8 Rennreife erhält, muss sie einen Dauerlauf auf den dynamischen Prüfständen absolvieren. In München arbeitet die jüngste Generation von Prüfanlagen für Motor und Getriebe. Die ultimative Anforderung für die Renntauglichkeit: 1.500 Kilometer mit einem synthetischen Streckenprofil, das die härtesteten Belastungsfälle der aktuellen Rennstrecken simuliert.
Motoren, die für den Transport zum Austragungsort bestimmt sind, absolvieren auf den Prüfständen einen schonenderen Funktionscheck. Danach findet noch eine Qualitätskontrolle inklusive Ölprobenuntersuchung auf etwaige Metallrückstände im Spektrometer statt. Dann ist Dienstantritt.
BMW lernt auf der Rennstrecke für die Straße
Synergien zwischen F1- und Serienentwicklung herzustellen, war für BMW die Grundvoraussetzung für den Wiedereinstieg zum Jahr 2000. Konsequent wurde die Entwicklung des Formel-1-Antriebsstrangs und der Elektronik am Standort München integriert. Dabei spielt das BMW Forschungs- und Innovationszentrum (FIZ) eine Schlüsselrolle.
Die F1-Fabrik wurde in weniger als einem Kilometer Entfernung von dieser Denkwerkstatt errichtet und mit ihr vernetzt. "Das FIZ repräsentiert die Zukunft von BMW", erklärt Theissen, "dort arbeiten die fähigsten Ingenieure in modernsten Forschungs- und Entwicklungseinrichtungen. Das FIZ verfügt über enorme Ressourcen, von denen wir unmittelbar profitieren. Umgekehrt stellt das F1-Engagement durch die extremen technischen Anforderungen und das geforderte Entwicklungstempo ein einzigartiges Versuchsfeld für unsere Techniker dar."
Das erworbene Know-how bleibt im Unternehmen, wo es der Serienentwicklung zugute kommt. Das für die Formel 1 entwickelte Wissen für die Bearbeitung von verschiedenen Materialien und Komponenten, beispielsweise von Zylinderköpfen und Kurbelgehäusen, wird für Serien-Pkw ebenso genutzt wie in der BMW Sparte Motorrad.
Gusstechnologien für die Formel 1 und für die Serie
Die Leistungsfähigkeit und Standfestigkeit von Motorblock, Zylinderkopf und Getriebe hängt entscheidend von der Gussqualität ab. Fortschrittliche Gusstechnologien mit höchst genauer Prozessführung ermöglichen leichte Bauteile von hoher Steifigkeit. Um dies für Serienfahrzeuge zu gewährleisten, unterhält BMW eine Gießerei in Landshut. Bereits 2001 wurde ihr eine eigene F1-Gießerei angegliedert. Beide Abteilungen arbeiten unter einer gemeinsamen Führung. Das garantiert den permanenten Austausch.
Mit dem gleichen Sandgussverfahren, mit dem der Formel-1-V8 entsteht, werden Ölwannen für die M-Modelle, die Sauganlage für den Achtzylinder-Dieselmotor sowie die Prototypen künftiger Motorgenerationen gegossen.
Fast zeitgleich mit der Inbetriebnahme der F1-Gießerei wurde nach demselben Modell eine F1-Teilefertigung an jene für Serienkomponenten angeschlossen. Dort fertigt das F1-Team unter anderem die Nockenwellen und die Kurbelwellen für die Formel 1.
Laborarbeit für die Zukunft
Die modernen Laboreinrichtungen des FIZ ermöglichen Materialforschung auf höchstem Niveau und im Schulterschluss mit den Formel-1-Experten. Dabei kommt der Entwicklung von Beschichtungen ein großer Stellenwert zu, aber auch für die Detektivarbeit der Schadensanalyse wird das High-Tech-Zentrum genutzt.
Bei der Forschung dient oft die Luft- und Raumfahrttechnik als Ausgangs¬basis. Einige viel versprechende Entwicklungen, die aus Kostengründen noch nicht für Großserien in Betracht kommen, haben im F1-Projekt bereits Verwendung gefunden. Diese Einsatzmöglichkeit neuer Technologien hilft den Ingenieuren, sie zur Serienreife weiterzuentwickeln.
Schnelle Modelle aus dem FIZ - Rapid Prototyping
Eine neue Idee, die Konzeptionsphase, der Konstruktionsvorgang, die Produktion notwendiger Werkzeuge, die Fertigung des neuen Teils, die Erprobungsphase - das ist der kosten- und zeitintensive Vorgang für Neuerungen. Weil in der Formel 1 extrem kurze Reaktionszeiten für Fortschritt und Problembewältigung gefordert sind, sucht man nach Abkürzungen. Auch hier kann die BMW Formel-1-Mannschaft auf das FIZ zugreifen, konkret auf die Abteilung Rapid Prototyping/Tooling Technology.
Sobald die benötigten Teile auf einem CAD-System konstruiert wurden, produzieren ebenfalls von Computern gesteuerte Maschinen mittels Laserstrahlen oder dreidimensionaler Drucktechnik maßgetreue Modelle aus Harz, Kunststoffpulver, Acrylat, Wachs oder Metall. Damit können kurzfristig Einbausituationen und Wechselwirkungen simuliert werden, um vor dem endgültigen Herstellungsprozess noch Modifikationen vornehmen zu können.
BMW P86/8 - technische Daten:
Bauart: 8-Zylinder-V-Saugmotor
Bankwinkel: 90 Grad
Hubraum: 2.400 ccm
Ventile: vier pro Zylinder
Ventiltrieb: pneumatisch
Motorblock: Aluminium
Zylinderkopf: Aluminium
Kurbelwelle: Stahl
Ölsystem: Trockensumpfschmierung
Motorsteuerung: Standard-ECU (MES)
Zündkerzen: NGK
Kolben: Aluminium
Pleuelstangen: Titan
Maße:
Länge 518 mm
Breite 555 mm
Höhe 595 mm (insgesamt)
Gewicht: 95 kg
Maximale Drehzahl: 19.000 U/min

