Folge uns jetzt auf Instagram und erlebe die schönsten und emotionalsten Momente im Motorsport zusammen mit anderen Fans aus der ganzen Welt
Zu Besuch im "Fort Knox" von Michelin
Ein hochinteressanter Einblick hinter die Kulissen der Entwicklung und Produktion von Michelin-Rennreifen für die Formel 1
(Motorsport-Total.com) - Sie sind schwarz, rund und entscheiden in der Formel 1 über Sieg und Niederlage: Damit Rennpneus und Grand-Prix-Boliden zu einer siegfähigen Kombination werden, müssen die Reifen-Ingenieure von Michelin viel Know-how in die Konstruktion und Entwicklung investieren. Wir warfen eine Blick hinter die Kulissen des Werks C4, in dem der französische Reifenspezialist unter größter Geheimhaltung das "schwarze Gold" für seine fünf Partnerteams BMW-Williams, Jaguar-Cosworth, McLaren-Mercedes, Renault und Toyota backt.
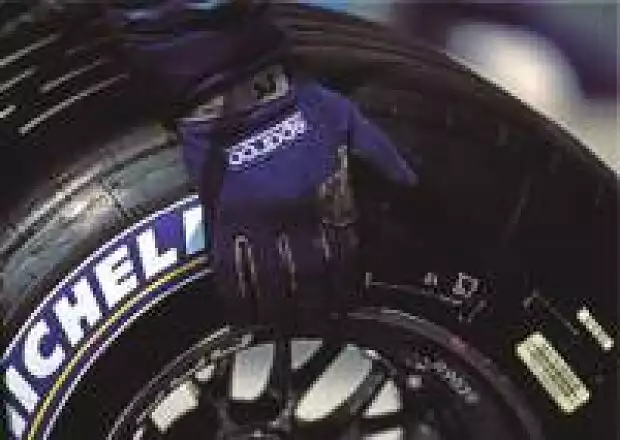
© Imago
Das "schwarze Gold" steht seit Neuauflage des Reifenkriegs im Mittelpunkt
Eine Besuchserlaubnis für das Reifenwerk von Catarou ist ähnlich leicht zu erhalten wie ein Gastflug zum europäischen Weltraumlabor ISS. Der unscheinbare Bau unweit des Stammwerkes in Clermont-Ferrand gehört zu den geheimsten und geheimnisvollsten Einrichtungen des französischen Herstellers. Denn im sogenannten C2-Werk, wo in der vergangenen Saison nicht weniger als 50.000 Grand-Prix-Reifen praktisch in Handarbeit zusammengefügt und gebacken wurden, mündet das gesammelte Know-how von Michelin in einzigartige Technologieträger: Auch sie sind ? wie fast jeder Reifen auf dieser Welt ? schwarz und rund, doch sie entscheiden über Sieg oder Niederlage und ermöglichen nicht selten Wettbewerbsvorteile von mehr als einer Sekunde pro Runde, während Modifikationen am Motor, dem Chassis oder der Aerodynamik eines Formel-1-Rennboliden allenfalls Verbesserungen im Zehntelbereich zulassen.
Gemeinsamkeiten zwischen Formel 1 und Serie
Das Erstaunliche jedoch ist: Auch wenn Serien- und Formel-1-Pneus grundlegend unterschiedliche Anforderungen erfüllen müssen, so basieren sie nicht nur auf demselben Konstruktionsprinzip, sondern werden sogar auf vergleichbare Art und Weise hergestellt. Dies beginnt schon bei der Wahl der Ingredienzen: Mehr als 200 unterschiedliche Materialien und Substanzen sind notwendig, um einen Reifen herzustellen ? darunter Öle, Stahl und Schwefelverbindungen, Kevlar, Polyester und bis zu 80 verschiedene Kautschuksorten, Aramide, Zink und Harz sowie eine gefällte Kieselsäure namens Silica. Da bei Rennreifen jedes einzelne Gramm als Teil der rotierenden Massen extrem ins Gewicht fällt, besitzen die Formel-1-Pneus von Michelin einen besonders hohen Anteil extra leichter Materialien wie Kevlarfasern als Stahlersatz oder auch textile Werkstoffe. Egal ob natürlich oder synthetisch gewonnen, die Quote des verbauten Kautschuks bleibt mit 79 Prozent praktisch identisch.
Riesige Maschinen vermengen den Kautschuk unter großer Hitze und enormem Druck sowie der Beigabe verschiedener Zutaten zu einem Grundgummi-Gemisch, das nach dem Abkühlen flach gewalzt und in so genannten Zerlegemühlen zu schmalen Streifen geschnitten wird. Diese Streifen werden anschließend Stück für Stück auf eine rotierende Trommel mit flexiblem Innenteil gespannt, wo sie einen Teil der Karkasse und die Seitenwand bilden. Zur Verstärkung fügen die Reifenbauer abwechselnd immer wieder einzelne Fadenmatten aus Kevlar- oder Carbonseilen hinzu. Die unterschiedlichen Fadenwinkel, in denen sie zueinander liegen, machen die Radial-Konstruktion des Pneus aus und gewähren dem Reifen Halt.
Vulkanisierung dauert zwölf bis 25 Minuten
Zieht sich das flexible Innenteil der Rotationstrommel zusammen, stülpt sich der Reifen zu seinem typischen U-Profil auf. Nachdem noch ein dickerer Kautschukstreifen mit der Lauffläche hinzugefügt wurde, wandert das "Greentire" genannte Konglomerat in den Vulkanisator. In dieser thermischen Formpresse erhalten Serienreifen wie Formel-1-Pneus zwölf bis 25 Minuten lang unter hohem Wasserdruck und bei einer Temperatur von bis zu 300 Grand nicht nur ihr Profil, es findet auch eine chemische Reaktion statt. Die eingesetzten Materialien verändern sich von einem plastischen zu einem elastischen Werkstoff.
Verläuft die Produktion von Straßenpneus nahezu vollautomatisch und mit einer Fehlerquote von deutlich weniger als einem Prozent, so werden die Formel-1-Reifen praktisch in Handarbeit gefertigt. Der Zeitaufwand beträgt rund zwei Mannstunden pro Pneu. Jeder zweite von ihnen wird ungebraucht wieder vernichtet, denn erfüllt eine Mischungs- und Konstruktionskombination auf der Strecke nicht die Erwartungen, wandert die komplette Baureihe in die Verbrennungsanlage ? wo auch gebrauchte Pneus landen, bevor sie als Technologieträger in falsche Hände geraten könnten. Den durchschnittlichen Grand-Prix-Bedarf zum Beispiel für das BMW-Williams-Team, also 20 Satz Rennpneus, fertigen die Spezialisten von Michelin in weniger als einem Tag ? sozusagen "a point". Dadurch kann der französische Spezialist innerhalb kürzester Zeit auf neue Erkenntnisse ? zum Beispiel von Testfahrten ? umgehend reagieren.
Reifenreglement in der Formel 1 sehr restriktiv
Geht der Trend für Pneus im normalen Automobilbereich zu immer höheren Innendurchmessern von 19 Zoll und mehr, so verharrt die Formel 1 eigentlich anachronistisch bei 13 Zoll hohen Felgen und wahren Ballonreifen. Der Hintergrund liegt klar auf der Hand: Einerseits muss das "schwarze Gold" wichtige Federungsaufgaben übernehmen, anderseits wollen die Reglementmacher durch diese Beschränkung eine Eskalation von Bremsleistungen verhindern. Wer die Lauffläche eines Grand-Prix-Pneus im Querschnitt betrachtet, erkennt, wie dünn und sparsam Michelin den Materialeinsatz dosiert. Der Grund: Je dicker die Lauffläche dimensioniert wird, desto stärker kann das Gummi in sich arbeiten. Die Folgen wären gefährliche Hitzenester in der Lauffläche, die eine konstante Performance des Rennreifens vereiteln.
Doch woher schöpft der Reifen seine Leistungsfähigkeit? Vereinfacht dargestellt, zeichnet die Laufflächenmischung ("Compound") ursächlich für den Grip auf der Strecke verantwortlich. Faustregel: Je weicher, desto haftfähiger ? aber auch umso verschleißfreudiger, wobei die Abnutzung selbst nur zum Teil von der reinen Laufleistung abhängt ? Parameter wie Fahrbahnoberfläche, Fahrweise und Fahrwerkseinstellungen bedingen die Dauerhaltbarkeit maßgeblich. Selbst ein sogenannter "aggressiver" Straßenbelag, der mit einem hohen Grip-Level aufwartet, stellt für den Compound prinzipiell kein Problem dar. Schwierig wird es erst, wenn Schlupf auftritt: Sobald der Reifen über die raue Oberfläche "radiert", heizt er sich auf und überhitzt im schlechtesten Falle.
Karkasse bestimmt Lenkverhalten, Stabilität und Haltbarkeit
Die Karkasse ? deren jeweilige Konstruktionsdetails geheim gehalten werden wie der Zugangscode zu Fort Knox ? bestimmt nicht nur das Einlenkverhalten, sondern auch die Seitenstabilität und die Dauerhaltbarkeit des Pneus. Diese Grundstruktur mit dem darüber liegenden Gürtel trägt über die Zugfestigkeit der Karkass-Seile und in Verbindung mit dem Luftinnendruck das Gewicht des Autos. Dabei hängt die Auslegung der Karkasse nicht allein von der jeweiligen Radlast ab, sondern auch von den Leistungsreserven des Fahrzeugs. Mit zunehmender Power wächst die Nachfrage nach geschmeidigeren Karkassen.
Genau wie bei Straßenreifen kennt diese spezielle, als Radial-Prinzip bekannte Form der Gürtellagenwickelung, die Michelin 1979 bei seinem Debüt in der Formel 1 erstmals im Rennsport einführte, bis heute keine Konkurrenz. Viele dieser Technologien wie zum Beispiel die "Null-Grad-Abdeckung" haben ihren Weg allerdings bereits in die Serie gefunden ? so besitzt auch der Michelin-Pilot-Reifen diese besondere Lage aus zugfesten und besonders leichten Kevlar- und Rayon-Fasern, die den Gürtel in Laufrichtung überspannt und unter hohen Drehzahlen ? also bei großen Fliehkräften ? ein "Wachsen" des Pneus verhindert.
Höherer Verschleiß durch Traktionskontrollen
Die elektronisch geregelten Traktionskontrollen wirken sich dabei erstaunlicherweise überaus verschleißfördernd aus: "Sie erlaubt Kurvenfahrt am Limit mit einem konstanten Schlupfverhältnis", erläuterte Pascal Vasselon, bei Michelin als Projektleiter verantwortlich für den Grand-Prix-Sport. "Die Fahrer bekämen dies manuell so exakt nicht hin und müssten immer wieder korrigieren. Gehen sie vom Gas, erhält der Reifen sofort eine kleine Rekreationspause."
Doch selbst in der Formel 1 scheint nicht ausschließlich die Sonne ? wie der Große Preis von Brasilien in dieser Saison eindrucksvoll bewiesen hat. Standen bislang so unterschiedliche "Wet-Weather"-Spezialisten wie der Intermediate für gemischte Verhältnisse, der eigentliche Regenreifen sowie der sogenannte Monsun-Pneu für wolkenbruchartige Niederschläge den Grand-Prix-Rennställen zur Verfügung, so darf Michelin seit Beginn der Saison 2003 den Teams pro Rennwochenende nur noch einen dieser Schlechtwetter-Experten anbieten. Entgegen der weitläufig verbreiteten Meinung basieren diese speziell profilierten Regen-Pneus im Übrigen nicht auf den Rillen-Slicks, sondern stellen eine ganz eigene Produktfamilie mit spezieller Karkasse und viel weicheren Laufflächenmischungen dar. Sie funktionieren bereits bei 40 bis 50 Grad Betriebstemperatur, würden auf trockenem Asphalt aber binnen weniger Runden völlig überhitzen.
Seit Beginn der Saison 2002 darf Michelin für jedes seiner fünf Partnerteams individuell je zwei verschiedene Formel-1-Pneus pro Grand-Prix-Wochenende anbieten. Die befürchtete Kostenexplosion jedoch blieb aus: "Ein guter Reifen ist für jedes Auto ein guter Reifen", erläuterte Pascal Dupasquier, der charismatische Sportdirektor von Michelin, die ausgebliebene Inflation. "Fünf unterschiedliche Karkass-Konstruktionen ? das wäre der Wahnsinn", pflichtete ihm Vasselon bei. Dann würden ihm streng abgeschirmten C2-Werk von Catarou die Lichter vermutlich überhaupt nicht mehr ausgehen...
Technische Daten eines Formel-1-Pneus
Optimale Betriebstemperatur: 100 Grad Celsius
Optimaler Luftdruck: 1,1 bis 1,2 bar vorn und 1,0 bis 1,1 bar hinten
Luftfüllung: Mit Stickstoff oder entfeuchteter Luft
Maximale Reifenbreite vorne/hinten: 355/380 mm
Felgendurchmesser: maximal 330 mm (13 Zoll)
Profilierung: vier symmetrisch umlaufende Rillen
Rillenbreite Tal/Oberfläche: 10/14 mm
Rillentiefe: 2,5 mm

