Renaults Formel-1-Fabrik in Enstone
Keith Saunt leitet die Formel-1-Fabrik von Renault in Enstone und erklärt Ihnen, wie der Alltag seines Teams aussieht
(Motorsport-Total.com) - Im Grunde genommen ist ein Formel-1-Auto wie der neue Renault R25 nicht viel mehr als ein gigantisches Puzzle mit 3.000 Teilen. Jedes einzelne davon wurde im Hinblick auf optimale Leistungsfähigkeit entworfen, produziert und anschließend gemäß den extrem strengen Qualtitätsstandards im RenaultF1-Workshop in Enstone kontrolliert.
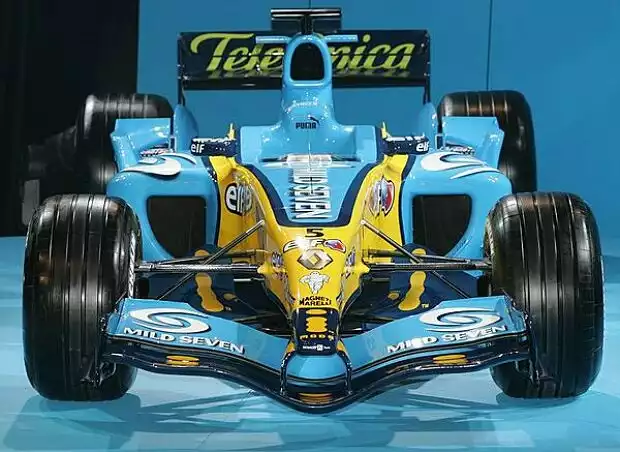
© xpb.cc
Der Renault R25 besteht aus rund 3.000 Einzelteilen
Noch bevor der R25 zum ersten Mal auf einer Rennstrecke fuhr, flossen bereits unzählige Arbeitsstunden und enormer Einsatz in seine Entwicklung. Beispiele gefällig? Bevor der gelb-blauen Bolide erste Gestalt annahm, fertigte die Entwicklungsabteilung in Enstone bereits rund 7.400 Komponenten- und Werkzeug-Zeichnungen für den Monoposto. Bis das erste Chassis fertig gestellt wurde, inspizierte, registrierte und lagerte das Team rund um Produktionsabteilungsleiter Keith Saunt insgesamt 48.200 Teile.#w1#
Bis zum Ende der Saison 2005 werden übrigens ungefähr 4.000 weitere Produktionszeichnungen entstehen. Welche Anforderungen diese unglaublichen Zahlen an Saunt und seine Mitarbeiter stellen? Die Antwort ist einfach: perfekte Organisation und die Fähigkeit zu vorausschauender Planung.
Methodisches Arbeiten, Disziplin und Organisation
Die 135 Mitarbeiter der Produktionsabteilung in Enstone müssen vor allem Prioritäten setzen können. So müssen Teile nicht nur für die Forschungs- und Entwicklungsabteilung in ausreichender Stückzahl produziert werden, sondern auch um die Bestände aufzufüllen oder für bevorstehende Testfahrten und Grands Prix. "Für jedes Teil erstellen wir eine Produktionsklassifizierung", erklärt Keith Saunt. "Dadurch erkennt jeder Mitarbeiter, welche Komponenten zu welcher Zeit benötigt werden."
Diese Liste befindet sich in einer so genannten UDSC-Datei (Usage, Damage, Shortage, Crossover = Einsatz, Beschädigung, Engpass, Überschneidung) gespeichert. Dieses System zeichnet sich unter anderem durch seine enorme Flexibilität aus. "Sobald die Designer eine Entwurfszeichnung fertig stellen, geht diese direkt an die Produktionsabteilung", erläutert Saunt.
"Wir legen dann einen Arbeitsauftrag an, der detailliert den Zeitpunkt festlegt, an dem das fertige Produkt benötigt wird. Anschließend bedienen wir uns eines ausgeklügelten System zur Feststellung des Arbeitsablaufs, das unter anderem die benötigte Zeit und die momentan in anderen Projekten genutzten Ressourcen mit einberechnet."
Für die Entwickler geht es also nicht nur darum, absolut leistungsfähige Teile zu entwerfen - sie müssen vielmehr auch den Produktions- und Zeitaufwand sowie den daraus resultierenden möglichen Einsatzzeitpunkt beachten. Aber genau das entspricht dem Charakter der Formel 1: Die unbestechliche Stoppuhr bestimmt das Geschehen und entscheidet über den Erfolg. "Beim RenaultF1-Team besitzt das optimale Ergebnis stets Vorrang vor einem möglicherweise vereinfachten Produktionsablauf", so Saunt.
"Jedes einzelne Teammitglied arbeitet extrem professionell. Und durch unsere lange Erfahrung können wir potenzielle Probleme oftmals bereits in der Entwicklungsphase ausschließen. Wir spielen auch bei jeder Entwicklung verschiedene Varianten durch. Aber mit unseren vielfältigen Möglichkeiten und Kenntnissen werden wir niemals Kompromisse eingehen."
Unverhofft kommt oft
Der RenaultF1-Workshop muss jederzeit auf veränderte Anforderungen reagieren: So kann es durchaus passieren, dass die Produktion einzelner Teile unterbrochen werden muss, weil sich eben diese Komponenten während einer Testfahrt oder einem Rennwochenende als fehlerhaft erwiesen. Aus diesem Grund wird die UDSC-Datei stetig aktualisiert. "Abhängig von den Schwierigkeiten, die auftreten, müssen wir zum Teil in Rekordzeit neue Entwicklungen produzieren", fährt Saunt fort.
"Wir geben uns immer jede erdenkliche Mühe, diesen Anforderungen gerecht zu werden. Unser Ziel lautet, dass der Renault R25 so leistungsfähig wie möglich ist. Wenn uns ein Notruf des Test- oder Rennteams erreicht, entscheiden wir daher sofort: machen oder kaufen? Dass heißt, wir überlegen, ob wir die Teile selber herstellen oder lieber bei einem Zulieferer bestellen."
Für weniger spezielle Komponenten oder aus Zeitgründen vertrauen die Experten in Enstone zum Teil auf externe Partner. "Insgesamt arbeiten wir mit 59 verschiedenen Zulieferern zusammen, die wir alle in einem Lieferanten-Bewertungssystem führen", verrät Saunt. "Dies erfasst Produktqualität, Zuverlässigkeit und sogar ihren Verwaltungsaufwand. Das System stellt also sicher, dass wir nur mit den Besten zusammenarbeiten."
Bei allem Zeitdruck achtet Saunt übrigens immer darauf, dass genügend Zeit für strenge Qualitätskontrollen eingeplant wird. Die zunehmende Bedeutung der Zuverlässigkeit in der Formel 1 macht zum Beispiel Überprüfungen von Teilen mittels ultraviolettem Licht unerlässlich. Rund 75 Prozent der Teile des Renault R25 entsteht übrigens direkt im RenaultF1-Workshop in Enstone. "Welche Voraussetzungen ich in meinem Job vor allem mitbringen muss? Nun, zunächst ein gutes Gedächtnis und viel Sinn für Humor", lacht Saunt. "Habe ich eigentlich das gute Gedächtnis bereits erwähnt...?"

