Der Fahrer-Faktor bei der Aerodynamik-Entwicklung
Red Bull Racing-Chefaerodynamiker Ben Agathangelou erklärt die Vorgehensweise des Teams bei der Entwicklung aerodynamischer Komponenten
(Motorsport-Total.com) - Es gibt ganz bestimmte Elemente, die die Grundlage der meisten Testfahrten bilden: Das Auto muss den Wünschen und Vorstellungen des Piloten entsprechend abgestimmt werden. Außerdem wird das streckenspezifische Setup ausgetüftelt. Der Motor muss Kilometer abspulen, und schließlich gilt es - das ist bei Neukonstruktionen ganz besonders wichtig -, der Effizienz des kompletten Aerodynamik-Pakets auf den Zahn zu fühlen.
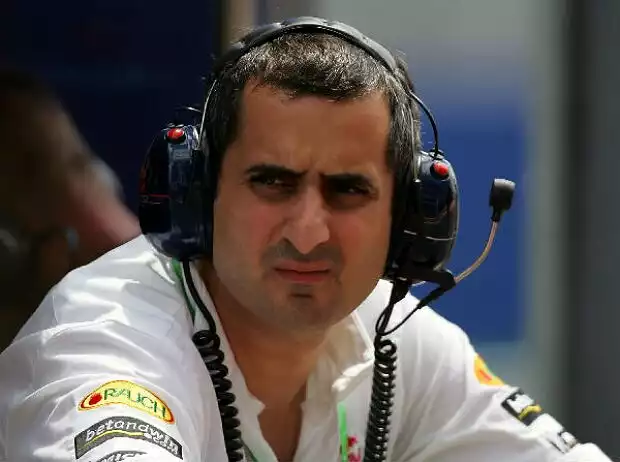
© Red Bull Racing
Ben Agathangelou vertraut den Fahrern immer noch mehr als dem Computer
Red Bull Racing-Chefaerodynamiker Ben Agathangelou erklärt auf der Internetseite des Teams am Beispiel des Frontflügels, wie das Team bei den Tests vorgeht: "In der Formel 1 gibt es unterschiedliche Denkansätze. Einige Teams kümmern sich darum allerdings gar nicht erst. Sie gehen grundsätzlich davon aus, dass sie sich bei ihrer Arbeit auf beste Windkanal-Daten verlassen können. Das gibt ihnen ausreichend Zuversicht, um einen Flügel aus dem Werk direkt mit an eine Rennstrecke zu nehmen, um ihn dort im Training auszuprobieren."#w1#
"Hier bei Red Bull Racing neigen wir zu wissenschaftlich fundierten Experimenten. Wenn es um einen neuen Flügel geht, hat man zunächst einmal die Daten aus dem Windkanal und vom Computational Fluid Dynamics. Ein neues Bauteil nehmen wir dann mit zu einem Test und probieren es im praktischen Fahrbetrieb aus, um mehr über seine charakteristischen Eigenschaften zu lernen."
"Viele der Daten, die uns bei einem solchen Test vorliegen, ergeben sich während der Arbeit vor Ort", so Agathangelou weiter. "Mit Blick auf ein aerodynamisches Bauteil suchen wir dann zunächst einmal Daten, die unsere Erkenntnisse aus dem Windkanal bestätigen. Wenn es beim Vergleich zu Übereinstimmungen kommt, haben wir allen Grund anzunehmen, dass das Teil tatsächlich die erwarteten und gewünschten Auswirkungen auf das Fahrverhalten hat."
Trotz dieses Hightech-Einsatzes sind die Aussagen der Rennfahrer oft ebenso wertvoll wie die Computer-Daten: "Der Pilot kann Veränderungen des Fahrverhaltens beschreiben, die auf eher abstrakten Entwicklungs-Methoden basieren - wenn es um Verbesserungen geht, lassen sich stets einige Details exakt messen, andere sind eher subjektiver Natur. Aus diesem Grund werden Entscheidungen teilweise aufgrund zuvor gesammelter Erfahrungen getroffen - was erwies sich als vorteilhaft, was nicht, und welchen Eindruck hatte der Fahrer?"
"Aufgrund dieser Daten-Analyse kann die Arbeit beurteilt werden, die während der Konstruktions-Phase geleistet wurde. Nachdem zuvor für den Test nur ein einziges Teil angefertigt wurde, entscheidet sich nun im Verlauf von Diskussionen mit dem technischen Direktor und anderen, ob das Teil für die 'Serienfertigung' geeignet ist oder nicht."
"Verlief alles zufriedenstellend, wird die Aerodynamik-Abteilung ihr offizielles Okay geben", fährt der Brite fort. "Dann wird im Werk mit der Produktion der Anzahl an Teilen begonnen, die für den Einsatz während eines Renn-Wochenendes gebraucht wird. Falls dann alles gut läuft, weiß man aufgrund der Daten-Analyse schon nach nur einem Testtag, was das neue Teil taugt."
Es ist unvermeidlich, dass Bauteile bei den ersten Tests zuweilen nicht den Erwartungen entsprechen. In solchen Fällen kann das Team sehr schnell reagieren. Am Beispiel der Endplatte des Frontflügels verdeutlicht dies der Aerodynamikspezialist: "Wenn es sich um eine simple Modifikation handelt, die zur Herstellung nur eine geringfügige Veränderung des Werkzeugs notwendig macht, dann hat man schon einen Tag nach Ende der Testfahrten eine Variante mit veränderter Geometrie parat. Neue Teile können dann umgehend produziert werden. Der Zyklus Analyse-Konstruktion-Freigabe nimmt wohl kaum mehr als drei, vier Tage in Anspruch."
"Aber normalerweise ist es so, dass man drei Frontflügel mit unterschiedlichen Eigenschaften testet und danach einen der möglichen Wege favorisiert. Anschließend werden die Unterschiede zwischen den drei Flügeln exakt analysiert, um sich für den weiteren Entwicklungsprozess des Flügels ein neues Ziel setzen zu können."
"Das kann fünf, sechs Wochen dauern, denn man muss ja zurück ans Reißbrett und von vorn anfangen - das ist etwas anderes, als ein existierendes Bauteil zu modifizieren. In solchen Situationen geht allerdings auch manchmal alles ganz schnell, weil man sofort eine Lösung vor Augen hat."

