Werde jetzt Teil der großen Community von Motorsport-Total.com auf Facebook, diskutiere mit tausenden Fans über den Motorsport und bleibe auf dem Laufenden!
Force India: Drei Mann und das Motorenklima
Schlanke Strukturen in der Formel 1: Bei Force India sind zwei Fachleute und ein Auszubildener für die Metallverarbeitung zuständig
(Motorsport-Total.com) - Der beste Mercedes-Motor wird kein Rennen überstehen, wenn die passende Kühlung nicht vorhanden ist. Dieser Fakt umschreibt recht genau, welche Verantwortung auf der nur drei Personen umfassenden Abteilung für Metallverarbeitung bei Force India lastet. Neil Christie zeichnet in der Fabrik in Silverstone gemeinsam mit einer weiteren Fachkraft und einem Auszubildenen unter anderem für die Herstellung der Kühler verantwortlich.
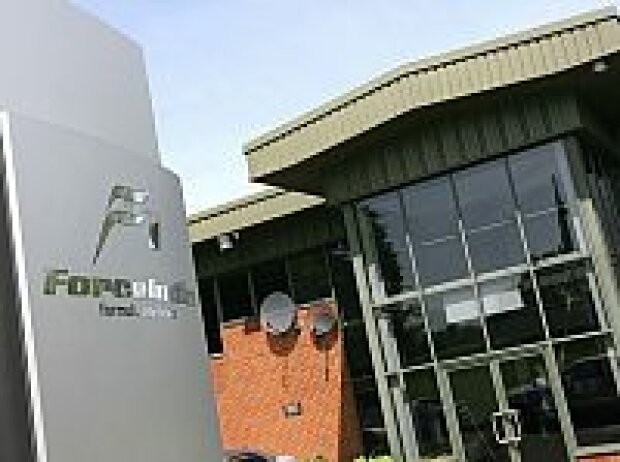
© Force India
Hinter der Fassade der Force-India-Fabrik wird am VJM02 gearbeitet
Der VJM02 von Force India wird aus den Teilen diverser Zulieferer zusammengebaut, unter anderem kommen im Rahmen eines neuen Deals der Motor, KERS und weitere Elemente des Antriebs von McLaren-Mercedes. Das Monocoque sowie weitere Chassisteile produziert die Verbundstoffabteilung, in der Metallverarbeitung werden einzig die Kühler, Auspuffteile, Ausstattungsteile der Box und Transportkisten gefertigt. "Prozentual ist unser Anteil am Auto sehr gering", erklärt Christie, "aber wenn wir etwas falsch machen, geht das Auto kaputt."#w1#
Heißes Eisen für kühlen Motor
"Wenn unsere Kühler nicht funktionieren, dann überhitzt der Motor und dann ist Schluss", stellte der Metallbauer die drastischen Auswirkungen eines Produktionsfehlers heraus. Seine Abteilung arbeitet eng mit den Konstrukteuren zusammen. Die entsprechenden Spezifikationen und Skizzen werden nicht nur vorgegeben, sondern notfalls auch gemeinsam mit den Ingenieuren verändert. "Wir müssen denen sagen, ob solche Bauteile rein physikalisch überhaupt herzustellen sind", sagt Christie.
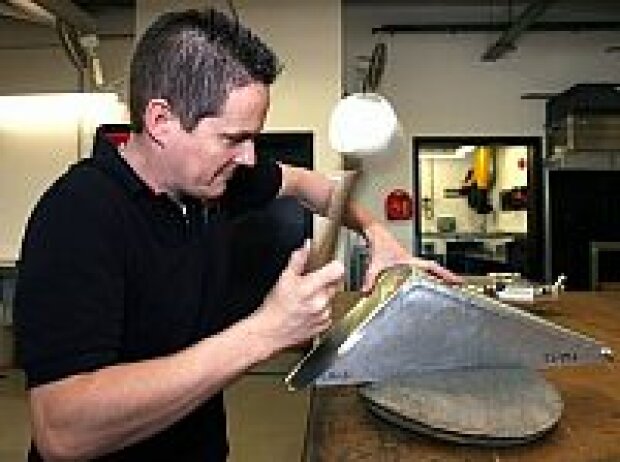
© Force India
In der Formel 1 gibt es nicht nur filigrane Techniken Zoom
Die "Drei von der Metallpresse", wie sie hausintern manchmal genannt werden, arbeiten zurzeit an den Modellen für den Windkanal. Weil die endgültigen Teile noch nicht fertig entworfen sind, stellen sie außerdem momentan Transportkisten für die Überseerennen her. "Wir sind ein wenig hinter dem Zeitplan zurück", gibt Christie zu. "Die Konstrukteure sitzen noch an den letzten Details." Unterdessen laufen die Porbeläufe für die neueste Kühlergeneration.
Nach der Herstellung der feingliedrigen Kühler werden die Neuteile zunächst mit Luft gefüllt und unter Druck gesetzt. Anschließend unterzieht man die Teile einem Test, den fast jeder Radfahrer schon einmal bei einer Reifenpanne vollzogen hat. "Wir halten die Kühler unter Wasser. Wenn es irgendwo ein Leck gibt, dann tritt Luft aus und wir können das anhand der Luftbläschen sehen", lacht Christie und fügt hinzu: "Nicht eben eine hoch wissenschaftliche Methode, aber wirksam."
Wie bei einem Fahrradschlauch...
Wenn die letzten Details für den VJM02 der Saison 2009 feststehen, legen die drei Mitarbeiter der Abteilung Extra-Schichten ein, um die Masse der Arbeit bewältigen zu können. Erst nach dem Start der Saison kommen wieder ruhigere Zeiten. "Wir stellen dann die Teile her, die aufgrund ihrer Haltbarkeit zwichendurch erneuert werden müssen. Nach jedem zweiten Rennen gibt es zum Beispiel neue Ölkühler. Die alten kommen zurück, wir reinigen und überprüfen sie und dann werden sie manchmal noch einmal verwendet."
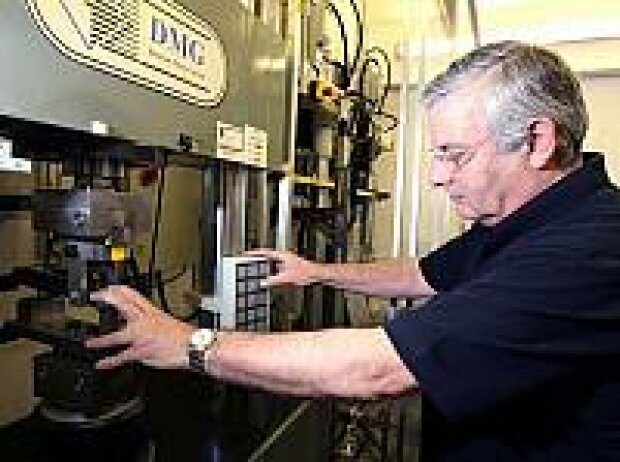
© Force India
In der Metallverarbeitung gehören aber auch Computersteuerungen zum Standard Zoom
Die Arbeit während der Saison ist berechenbarer, daher stellt man die Ersatzteile "just in time" her. Es sei denn, der neue Bolide erweist sich als Gurke und es steht ein kompletter Neubau ins Haus. "Wenn man ein Re-Design hat, wir wir es mitten im Jahr 2007 erlebt haben, als eine B-Version gebaut wurde, dann fangen natürlich auch wir wieder neu an. Einige der neuen Teile werden dann radikal anders sein und das kostet natürlich alles Zeit."
"Ein normaler Ölkühler braucht insgesamt vier Tage für die Produktion", schildert Christie. "Man darf nicht vergessen, dass es darin zwei verschiedene Flüssigkeiten zu kühlen gilt. Zum einen das Motoröl und zum anderen das Getriebeöl. Beide Teile werden einzeln vorbereitet, dann zusammengefügt. Allein zwei Tage brauchen wir, um beide Kreisläufe zusammen zu installieren. Unsere größte Herausforderung ist es, alles punktgenau fertig zu bekommen. Aber wir schaffen das, denn auch wir wollen endlich Punkte sammeln..."

