Der Windkanal von BMW: Mehr als ein High-Tech-Werkzeug
Lesen Sie eine beeindruckende Reportage über die Leistung des Windkanals in Hinwil und dem dazugehörigen Supercomputer "Albert"
(Motorsport-Total.com) - "Die Aerodynamik macht rund zwei Drittel der Performance eines modernen Formel-1-Autos aus", sagt Willy Rampf. Entsprechend wichtig ist es, in diesem Bereich gut gerüstet zu sein. Auf der Suche nach Zehntelsekunden kann sich das BMW Sauber F1 Team auf einen der modernsten Windkanäle in der FormeI 1 verlassen.
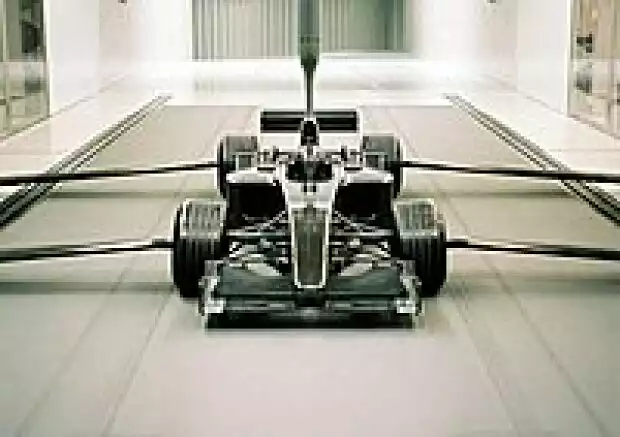
© xpb.cc
Ein Modell im Windkanal des BMW Sauber F1 Teams in Hinwil
In Bezug auf Faktoren wie Windgeschwindigkeit, Größe der Testsektion und der Modelle, Dimensionen der "Rolling Road", "Model Motion System" sowie Datenerfassung repräsentiert diese Anlage den neuesten Stand der Technik.#w1#
Der Windkanal ist als geschlossener Kreislauf ausgeführt, der eine Gesamtlänge von 141 Metern und einen maximalen Rohrdurchmesser von 9,4 Metern hat. Das Gewicht aller Stahlelemente beträgt inklusive Ventilatorgehäuse 480 Tonnen. Der einstufige Axialventilator mit Rotorblättern aus Karbon wiegt mit Antrieb und Verkleidung 66 Tonnen.
Bei Volllast nimmt der Hauptventilator eine Leistung von 3.000 kW auf und ermöglicht so Windgeschwindigkeiten bis zu 300 km/h. Damit keine störenden Schwingungen auf die Anlage übertragen werden, ist der Axialventilator über Schwingungsdämpfer mit einem massiven Betonsockel gekoppelt
Das Kernstück jedes Windkanals ist die Testsektion, wo die Objekte dem Luftstrom ausgesetzt werden. Sowohl deren Querschnitt als auch die Länge der rollenden Straße sind besonders großzügig ausgelegt und bieten damit optimale Voraussetzungen für genaue Resultate. Gearbeitet wird mit 60-Prozent-Modellen
Damit die Testobjekte nicht nur frontal, sondern auch leicht schräg bis zu einem Winkel von maximal zehn Grad angeströmt werden können, lässt sich die gesamte Messplattform drehen. Diese ist mit einem Stahlband ausgerüstet, das die Relativbewegung zwischen Fahrzeug und Straße simuliert. Das rotierende Stahlband erreicht die gleiche Geschwindigkeit wie die Luftströmung, also bis zu 300 km/h. Unter dem Rollband sind Wägezellen angebracht, mit welchen sich die Radlasten erfassen lassen.
Windkanäle wirken in der Regel von außen wenig attraktiv. Nicht so die Anlage in Hinwil, denn auch dem Erscheinungsbild wurde große Beachtung geschenkt. Das Gebäude beeindruckt nicht bloß durch seine Abmessungen (Länge 65 m, Breite 50 m, Höhe 17 m), auch die mit Glas verkleideten Fassaden machen seine Einmaligkeit als Kombination von Industriebau und Eventgebäude sichtbar.
Was von außen als homogene Halle erscheint, besteht in Wirklichkeit aus zwei klar abgetrennten Gebäudeelementen: dem eigentlichen Windkanal und einem mehrgeschossigen Trakt mit Arbeitsräumen und einer Eventplattform. Die beiden Bereiche werden durch eine Glaswand getrennt, so dass der optische Bezug erhalten bleibt, die Lärmemissionen des Windkanals aber wirkungsvoll abgehalten werden.
Aus optischen Gründen liegt die Mittelachse der Windkanalverrohrung mehr als acht Meter über dem Boden. Mit Aus¬nahme der Messstrecke, die in eine Betonkonstruktion eingebettet ist, "schwebt" der aus Stahlelementen zusammengefügte Kreislauf in der Halle. Großzügig konzipiert ist auch der zweite Gebäudeteil mit insgesamt vier Stockwerken. Die Galerie im ersten Stock bietet 150 Personen Platz.
Hier können Marketingveranstaltungen, Kundenevents oder Seminare in einer einzigartigen Atmosphäre durchgeführt werden. In den darüber liegenden Stockwerken befinden sich die Arbeitsräume für die Aerodynamiker, die Modelldesigner, Modellbauer, die CFD-Ingenieure sowie weitere Spezialisten der Aerodynamikabteilung. Dieser Windkanal ist in seinem Gesamtkonzept einzigartig.
"Albert" ist sehr berechnend
Die computergestützte Strömungssimulation bietet immer mehr Möglichkeiten bei der Berechnung von Aerodynamik-Komponenten, vorausgesetzt, man verfügt über eine sehr hohe Rechenkapazität. Das BMW Sauber F1 Team kann dabei auf einen Supercomputer zählen, der zu den leistungsfähigsten in der Formel 1 wie auch in der gesamten Automobil-Industrie gehört. "Albert", wie die Maschine heißt, wurde von der Schweizer Firma DALCO unter Verwendung von insgesamt 530 64-Bit-Prozessoren gebaut. Die Software stammt von Fluent.
CFD (Computational Fluid Dynamics), oder zu deutsch "computergestützte Strömungssimulation", dient der Berechnung von Aerodynamik-Komponenten und stellt eine wichtige Ergänzung zur Arbeit im Windkanal dar. "Die Aerodynamik hat in den letzten Jahren stetig an Bedeutung gewonnen. Damit ist auch die computergestützte Strömungssimulation immer wichtiger geworden", erklärt Willy Rampf.
Insgesamt beinhaltet der neue Supercomputer 530 Prozessoren in einer Cluster-Architektur mit Dual-Nodes, die in High-Density-Klima-Racks der Firma American Power Conversion (APC) untergebracht sind. Diese Racks sind autonom und verfügen über einen geschlossenen Wasserkreislauf, der eine Kühlleistung von bis zu 15 kW pro Rack ermöglicht. Der Supercomputer besteht aus insgesamt zehn Racks, die eine Breite von je einem Meter, eine Tiefe von 1,20 Metern und eine Höhe von 2,30 Metern haben. Daraus ergibt sich eine Gesamtbreite von zehn Metern. Das Gewicht beträgt 18 Tonnen.
Imposant sind jedoch nicht nur die harten Fakten, sondern auch die technischen Daten: Der Supercomputer verfügt über 2,3 Tflop/s, 1 TB RAM und 11 TB Plattenspeicher. Zur Erklärung für Nicht-Computer-Experten heißt das, dass "Albert" pro Sekunde 2.332.000.000.000 Rechenoperationen ausführen kann.
Für die gleiche Rechenleistung müssten die rund 350.000 Einwohner der Stadt Zürich während eines ganzen Jahres alle vier Sekunden zwei achtstellige Zahlen multiplizieren. Die Maschine verfügt über 1.085.440 MegaByte-Hauptspeicher sowie über 10.880 GigaByte Plattenspeicher für das System.
Genutzt werden die schier unbegrenzten technischen Möglichkeiten des Supercomputers für Analysen im Bereich der Aerodynamik. Mittels CFD werden am Computer Aerodynamikteile für die Formel-1-Renner berechnet. Dabei werden numerische Gitternetz-Modelle verwendet, die aus bis zu 100 Millionen Zellen bestehen. Diese hohe Auflösung ermöglicht es, die Modelle besonders fein zu definieren, was eine entsprechende Qualität der Resultate ergibt.
Weil dank "Albert" die Rechenzeiten sehr kurz sind, kann man viele verschiedene Varianten prüfen. Zudem lassen sich auch komplexe Fahrsituationen simulieren. CFD spielt eine wichtige Rolle bei der Entwicklung von Front-, Heck- und Zusatzflügeln sowie bei der Motor- und Bremskühlung.
Die computergestützte Strömungssimulation steht nicht in Konkurrenz zur Arbeit im Windkanal - ganz im Gegenteil. CFD und experimentelle Windkanalarbeit sind stark vernetzt und ergeben so Synergien, die beidseitig genutzt werden können.
Bei der Entwicklung eines neuen Frontflügels werden bis zu 100 Varianten zweidimensional geprüft, bevor dann rund ein halbes Dutzend in dreidimensionaler Form analysiert wird. Die vielversprechendsten Versionen werden anschließend für das 60-Prozent-Modell gebaut und getestet. CFD ermöglicht so eine besonders effiziente Nutzung des Windkanals.

