Hightech-Baustelle: Produktion des LMP1 in Köln
Im zweiten Teil unserer Serie über das Toyota-Engagement auf der Langstrecke blicken wir auf die Produktion des LMP1-Autos: Der Stoff, der aus der Kälte kam
(Motorsport-Total.com) - In der Le-Mans-Szene ist auch 2012 Spannung garantiert. Nach dem plötzlichen Rückzug von Peugeot sprang Toyota in die Bresche. Die Japaner mit Entwicklungsstandort in Köln machten aus dem geplanten Testjahr mit dem neuen TS030 Hybrid ein Einsatzjahr und verhalfen der neuen WEC zu mehr Wettbewerb. In unserer Serie stellen wir das Toyota-Projekt genauer vor. Heute: Die Produktion des Fahrzeugs in Köln-Marsdorf.
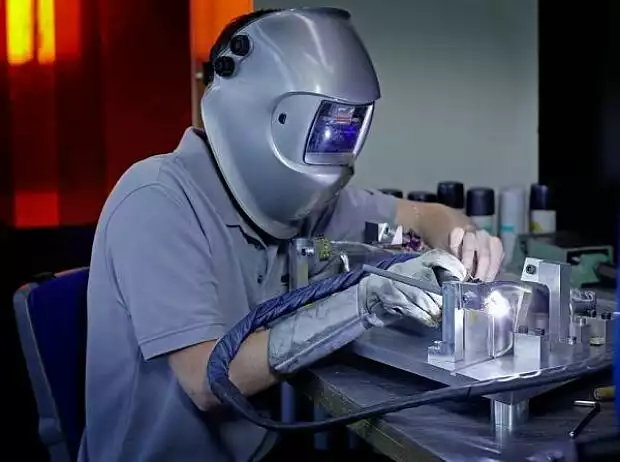
© Toyota
In der Produktion in Köln-Marsdorf gibt es noch viel Handarbeit Zoom
An einem angenehmen Sommernachmittag öffnen sich für mich die Türen zu den heiligen Hallen der Toyota Motorsport GmbH (TMG) in Köln. In den insgesamt rund 30.000 Quadratmeter großen Hallen des Unternehmens beleuchten Neonröhren die Szenerie. Die Mitarbeiter bekommen vom herrlichen Wetter draußen wenig mit, aber dennoch strahlen sie mit der Sonne um die Wette. Bei TMG sind alle Fachleute vom Motorsport-Virus befallen. Entsprechend viel Freude bereitet ihnen die Arbeit am neuen LMP1-Auto.
Mein Weg führt in die Produktionsabteilungen, die rund 7.400 Quadratmeter umfassen. 60 Mitarbeiter absolvieren dort die wichtigsten Schritte, damit aus CAD-Entwürfen echte Teile werden. An 18 CNC-Maschinen entstehen wichtige Bauteile des TS030, der in diesem Jahr in Le Mans für Furore sorgte. Die Leidenschaft, mit der die "Toyoten" in Köln ans Werk gehen, brandet mir direkt nach dem ersten Schritt in die Abteilung Produktion entgegen.
Mit Hingabe und Liebe bearbeiten Mitarbeiter einen glänzenden Krümmer, streichen zart über die Konturen von präzise geformten Blechen und nicken mir freundlich zu. Aus dem Hinterhalt nähert sich ein Fachmann mit einem kastenförmigen Konstrukt aus glänzendem Metall. "Hier", sagt er, "das ist der Kühler von Timo Glocks Formel-1-Auto nach dem Crash in Hockenheim 2008. Alles ineinandergeschoben, aber dicht. Nicht eine Schweißnaht hat eine Macke."
Handarbeit und große Fräsen
Ich betrachte das Bauteil, das für meine laienhaften Augen aussieht wie neu. Erst bei genauerem Hinschauen wird deutlich, dass der damalige Einschlag den gesamten Kühler in sich zusammengefaltet hat wie ein Schifferklavier am Ende eines Konzerts. Verbogen ja, aber kaputt? Nein. Voller Stolz stellt der Mitarbeiter das Vorzeigeobjekt wieder zurück in die Schatzkammer der Abteilung. Es wird schnell deutlich: Hier wird Handarbeit auf allerhöchstem Niveau abgeliefert.
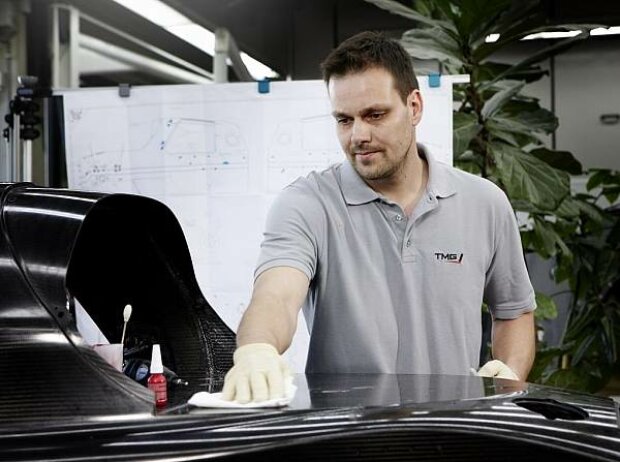
© Toyota
Nicht nur sauber, sondern rein: Beim Umgang mit Karbon ist Sauberkeit gefragt Zoom
"Benzin im Blut ist wichtig. Wir alle haben diesen Virus in uns. Wir fiebern in besonderer Form mit, denn dort fährt ein Auto auf der Strecke, zu dem wir eine innige Beziehung haben", bemüht sich Produktionsleiter Andreas Schambach die eben beschriebene Situation zu erklären. Er führt mich vorbei an den Hitech-CNC-Maschinen, die sich gerade mit äußerster Präzision über große Portionen von NE-Metallen hermachen. In den Regalen lagern Titan, Stahl, Alu und weitere Werkstoffe.
Die 60 erfahrenen Fachkräfte in der Produktion von TMG setzen die Dinge um, die sich Design und Konstruktion für das LMP1-Projekt haben einfallen lassen. Hier wird geformt, gebaut, gehämmert und mit großer Freude auf das fertige Produkt geschaut. Vier Messanlagen geben nach der Fertigstellung von Elementen präzise Auskunft darüber, ob sich alle Teile im Rahmen der vom Bereich Engineering geforderten Genauigkeit befinden.
Wenige Meter weiter folgt die Composite-Abteilung. In riesigen Fräsmaschinen entstehen aus Kunststoff jene Gebilde, die später als Form für den Bau der Carbon-Elemente dienen. Der Prozess der Formherstellung läuft vollautomatisch auf Grundlage der vorliegenden CAD-Daten. "Es muss bei uns alles haargenau passen. Das gilt nicht nur für unsere Teile für den LMP1-Wagem, sondern natürlich auch für all unsere Kunden", sagt Schambach.
Monocoque-Bau in Schutzatmosphäre
"Im Motorsport gehen alle an die Grenzen. Sollte dort auch nur ein Maß nicht hundertprozentig passen, dann kann es schon Probleme beim Vermessen mit den technischen Delegierten geben. Will keiner haben", lacht er. Deswegen gibt es bei TMG zwei Wege beim Bau von Carbon-Komponenten. Jene Elemente, die nur in geringer Stückzahl produziert werden, entstehen auf Basis der Kunststoffformen, bei allen anderen Teilen wird eine präzise Carbonform verwendet.
"Dieses Carbontool kostet dann vielleicht das Zehnfache, aber es bleibt immer im haargenau gleichen Maß", erklärt Schambach. "Früher mussten Teile noch geschmirgelt werden. Das muss man heutzutage nicht mehr. Wir haben neue Werkzeug-Technologien im Einsatz, die wir gemeinsam mit Werkzeug-Herstellern entwickelt haben. Dadurch erübrigt sich das nun." Beim Blick auf eine vormontierte LMP1-Frontpartie ergänzt er stolz: "Unser Auto hat keine Spaltmaße!"
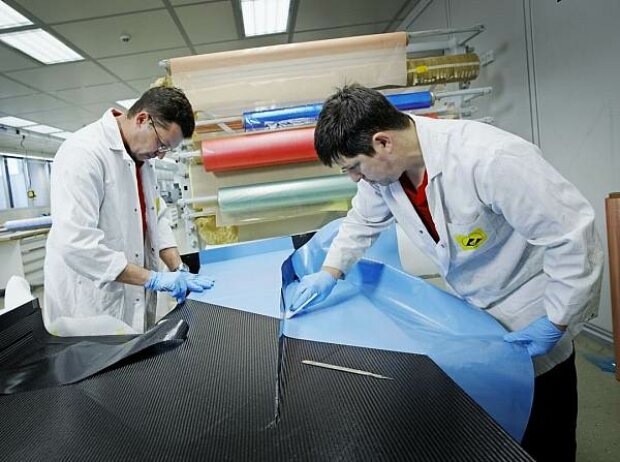
© Toyota
Die einzelnen Lagen von Karbon werden präzise geschnitten und verlegt Zoom
Der Nebenraum wird von Kunststoffbahnen verschleiert, es liegt ein Rauschen in der Luft. Durch eine Art Druckkammer geht es in das OP-Zentrum von TMG, dorthin, wo das Kernstück eines jeden Rennfahrzeuges entsteht: das Monocoque. "Den Druckkorridor haben wir, um Schwebepartikel fernzuhalten. Sonst hätte man womöglich Staub zwischen den Lagen. Das wäre nicht gut", schildert der Produktionsleiter und zieht mich mit einem freundlichen Lächeln zu Seite.
Ein Kollege trägt auf (Samt-)Handschuhen eine Kohlefasermatte vorbei. Der im Motorsport so heiß geliebte Werkstoff, der Festigkeit mit wenig Gewicht vereint, kommt aus der Kühlkammer. "Das Material wird bei minus 26 Grad eingelagert. Nach dem Auftauen haben wir rund drei Tage Zeit für die Verarbeitung, bevor es hart wird. Es ist dann nicht mehr homogen", erklärt Schambach. Kohlefaser hat quasi ein Verfallsdatum wie der Joghurt im heimischen Kühlschrank. "Ja, aber der Joghurt kostet nur ein paar Cent. Wenn uns hier der Werkstoff verkommt, dann wird es teuer", lacht der erfahrene Techniker.
Im Hintergrund arbeiten die Composite-Fachleute am Aufbau einer neuen LMP1-Kernzelle. "Ein Monocoque ist für mich ein Wunderwerk. Da steckt so viel Know-how drin, so viele handwerkliche Fähigkeiten, so viel Arbeit. Es ist das wichtigste Teil vom Auto. Alles baut sich daran auf", schwärmt Schambach beim Blick auf seine konzentrierten Kollegen. "Wir machen die obere und die untere Hälfte, die wir laminieren. Zwei Hälften haben den Vorteil, dass die Bearbeitung einfacher ist. Man muss innerhalb des Monocoques arbeiten, um die Teile zu verbinden."
Emotion pur: Die Fahrten in Le Mans
Bis die zwei Monocoque-Hälften verschraubt und über weitere Carbon-Lagen weiter verstärkt werden, sind unzählige Stunden Arbeit notwendig. Das Bauteil besteht zunächst aus mehreren Schichten ("Die werden alle von Hand eingelegt") des Kohlefaser-Werksstoffes, der mit höchster Präzision verarbeitet werden muss. Bei TMG zeigen Laser die optimale Positionierung der Matten haargenau an. "Der Vorteil ist, dass man eine extrem geringe Überlappung der Lagen hat. Dadurch spart man unter anderem auch Material."
"Viel wichtiger ist aber, dass das Bauteil dadurch möglichst leicht ist. Das kann bei einem Monocoque ein bis zwei Kilogramm ausmachen", schildert Schambach. Sind die ersten Schichten gelegt, folgen eine Waben-Struktur ("Honeycomb") sowie weitere Schichten Kohlefaser. Nachdem diese aufwändigen Arbeiten abgeschlossen sind, geht das Bauteil in den Autoklav, ein thermischer Druckbehälter, der für die nötige Festigkeit sorgt. Das Monocoque wird "gebacken".
"Das Monocoque für unser zweites Auto haben wir in nur sechs Wochen gebaut", sagt Schambach, der nach dem Testunfall von Nicolas Lapierre in Le Castellet gemeinsam mit seinen Kollegen im Schichtbetrieb arbeiten musste, damit Toyota bei den 24 Stunden von Le Mans überhaupt mit zwei Fahrzeugen antreten konnte. "Als wir den Wagen mit der Startnummer acht dann fahren gesehen haben, hatten viele Mitarbeiter Tränen in den Augen."
Leidenschaft und Hingabe ist das, was die gesamte Crew der Abteilung ausstrahlt. Die Formel 1 ist Vergangenheit, die Le-Mans-Szene die Gegenwart und Zukunft. Dies haben Schambach und seine Kollegen als neue Herausforderung angenommen. "Die Anforderungen mögen bei Formel 1 und Le Mans unterschiedlich sein, aber die Grundvoraussetzung ist gleich: Qualität muss stimmen. Bezüglich Präzision gibt es bei uns überhaupt keinen Unterschied zwischen dem Le-Mans-Wagen und der Formel 1."
Lesen Sie morgen den dritten Teil unseres Toyota-Features auf 'Motorsport-Total.com': Aerodynamikentwicklung und Simulation - wenn ein riesiger Ventilator einen Sturm entfacht und Alex Wurz in Abwesenheit seine Runden dreht.

